Слайды и текст этой онлайн презентации
Слайд 1
Обработка металлов - виды, способы и технологии металлообработки
Подготовил: Учитель Технологии
Ганин Виктор Сергеевич
Слайд 2
Многие столетия люди работают с металлами. Большинство материалов – прочные и твердые, требующие приложения усилий для изменения размера и формы. Для обработки металла используют разные станки и характерные приемы.
Слайд 3
Что такое металлообработка и для чего это нужно?
Обработка металла – технологический процесс, смысл которого заключается в физическом воздействии на материал: меняются характеристики, физические и механические свойства и размеры. Благодаря такому взаимодействию удается получить готовые детали.
Слайд 4
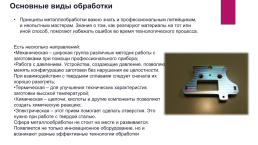
Основные виды обработки
Принципы металлообработки важно знать и профессиональным литейщикам, и неопытным мастерам. Знания о том, как реагируют материалы на тот или иной способ, помогают избежать ошибок во время технологического процесса.
Есть несколько направлений:
Механическая – широкая группа различных методик работы с заготовками при помощи профессионального прибора;
Работа с давлением. Устройства, создающие давление, позволяют менять конфигурацию заготовки без нарушения ее целостности. При взаимодействии с твердыми сплавами следует сначала их хорошо разогреть;
Термическая – для улучшения технических характеристик заготовки высокой температурой;
Химическая – щелочи, кислоты и другие компоненты позволяют создать химическую реакцию;
Электрическая – этот прием помогает сделать отверстия. Это нужно при работе с твердой сталью.
Сфера металлообработки не стоит на месте и развивается. Появляется не только инновационное оборудование, но и возникают разные эффективные технологии обработки
Слайд 5
Сверление и точение
Сверление – метод обработки металла, состоящий из этапов:
При помощи тисков и струбцин заготовку закрепляют на столе;
В патроне закрепляют оснастку для создания резьбы;
После запуска электрического двигателя шпиндель выкручивает патрон, за счет оснастки в заготовке образуется отверстие оптимального диаметра.
Поскольку сверла выдерживают различные нагрузки, при выборе оснастки ориентируются на свойства обрабатываемого сплава. Не менее распространенный тип обработки – точение. Такой технологический процесс позволяет создавать заготовки в виде конуса или цилиндра. Технология такова:
Закрепляют изделие в подвижном шпинделе;
Включается двигатель, выкручивается элемент;
Мастер при помощи резцов снимает слой.
При взаимодействии с токарными ЧПУ используют стандартный принцип работы с типами сверления. Такая методика позволяет сделать резьбу и изменить конфигурации изделия при помощи различных резцов. Чтобы не отравиться, мастера надевают защитные очки.
Слайд 6
Шлифование и фрезерование
Один из популярнейших типов – фрезерование: он немного схож со сверлением. Фреза позволяет создать резьбу и углубления в поверхностях, обработать торцы элементов, во время вращения шпинделя снимается верхний слой.
При обработке используют и абразивные материалы – метод шлифования: на подвижном валу фиксируют круг с напылением, электродвигатель ослабляет конструкцию. Тип работы зависит от абразива:
Небольшая фракция предназначена для заключительных работ;
Круги с большими частицами созданы для очищения поверхности от ржавчины.
Слайд 7
Токарная обработка
С детали снимают тонкие слои, пока она не достигнет конкретной шероховатости. Для работы используют режущие инструменты и станки. Этот тип схож с расклиниванием слоя острой кромкой инструмента. За счет механического усилия она врезается в изделие, снимая припуск, превращающийся в стружку.
Повышенная скорость резки и непрерывность процесса позволяют сделать результат работы еще более качественным. Важный момент: скорость резки подбирается индивидуально. С помощью токарного инструмента изготавливают валы, втулки, гайки, зубчатые колеса, кольца, муфты, шкивы.
Слайд 8
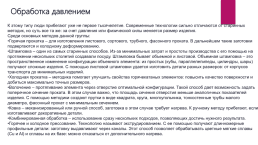
Обработка давлением
К этому типу люди прибегают уже не первое тысячелетие. Современные технологии сильно отличаются от старинных методик, но суть все та же: за счет давления или физической силы меняется размер изделия.
Среди основных методов данной группы:
Горячая прокатка – для изготовления листового, сортового, трубного, фасонного проката. В дальнейшем такие заготовки подвергаются и холодному деформированию.
Штамповка – один из самых старинных способов. Из-за минимальных затрат и простоты производства с его помощью на протяжении нескольких столетий создавали посуду. Штамповка бывает объемной и листовой. Объемная штамповка – это пространственное изменение конфигурации объемного элемента: из простых (кубы, параллелепипеды, цилиндры, шары) получают сложные изделия. С помощью листовой штамповки удается изготовить детали разных размеров: от корпусов транспорта до минимальных изделий.
Холодная прокатка – методика помогает улучшить свойства горячекатаных элементов: повысить качество поверхности и добиться максимально точных размеров.
Волочение – протягивание элемента через отверстие оптимальной конфигурации. Такой способ дает возможность задать поперечное сечение проката. В этом случае важно, что площадь сечения отверстия меньше аналогичных показателей изделия. С помощью методики создают прутки в виде квадрата, круга, многоугольника, тонкостенные трубы малого диаметра, фасонный прокат с минимальным сечением.
Ковка – механизированный или ручной способ, заготовка в этом случае требует нагрева. К ручному методу прибегают, если изготавливают декоративные детали.
Комбинированная обработка – использование сразу нескольких подходов, позволяющих достичь нужного результата.
Горячее и холодное прессование. Технологию называют экструдированием. С ее помощью получают длинномерные профильные детали: заготовку выдавливают через каналы. Этот способ позволяет обрабатывать цветные мягкие сплавы (Cu и Al) и сплавы на их базе: можно отказаться от дополнительного нагрева.
Слайд 9

Обработка металлов сваркой
Для соединения деталей в массовом и мелкосерийном производстве применяют сварку. При этом заготовки можно соединять углами, торцами, внахлест: предполагается нагрев материала до появления кромок или до температуры пластичности. Уже потом элементы соединяют в монолитную конструкцию. Существует три основных вида:
Газовый – перед резкой или сваркой сталь нагревают газовой горелкой.
Химический – температура повышается за счет химической реакции. Если нельзя использовать газовый баллон или электрическое оборудование, прибегают к этому виду.
Электрическая сварка – самый популярный метод, с помощью которого сначала нагревают, а затем плавят материал для последующего соединения.
Последняя группа подразделяется еще на два вида:
Контактная – бывает роликовая и точечная. В основе – нагревание электрическим током. При роликовом методе по поверхности стыка создают сплошной шов, при точечном детали соединяют в конкретных точках.
Дуговая – использование тепла электродуги. Для работы используют электроды (среда инертных газов) и сварочное оборудование.
Слайд 10
Спасибо за внимание!